Износ дышловых клиньев в местах прилегания к подшипнику или скобе допускается не более 0,5 мм и только в том случае, если клин
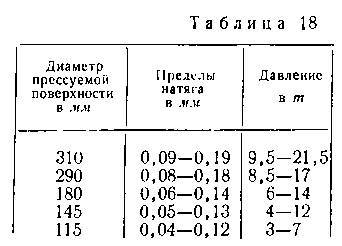
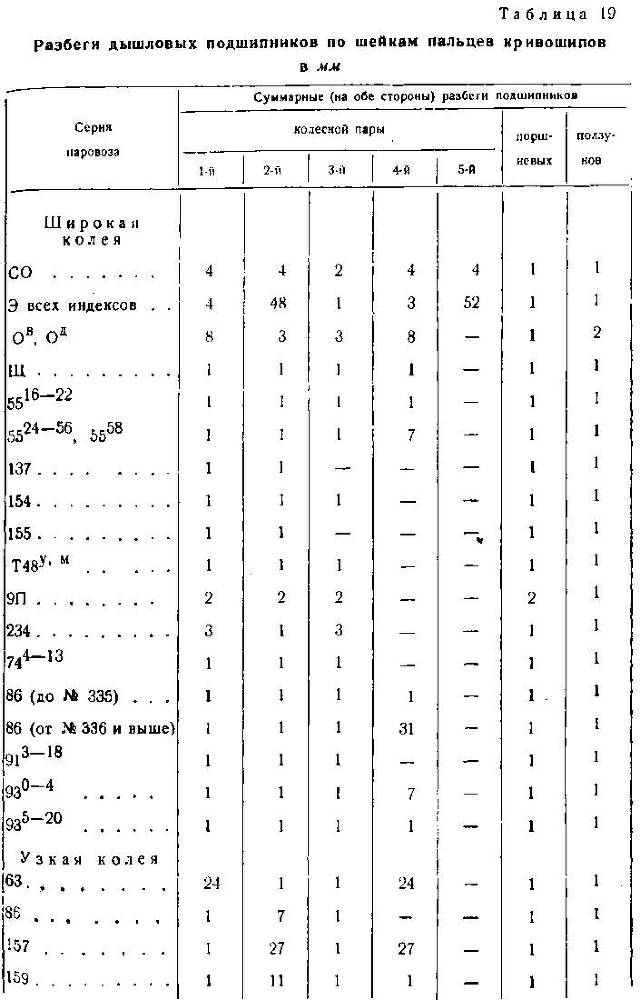
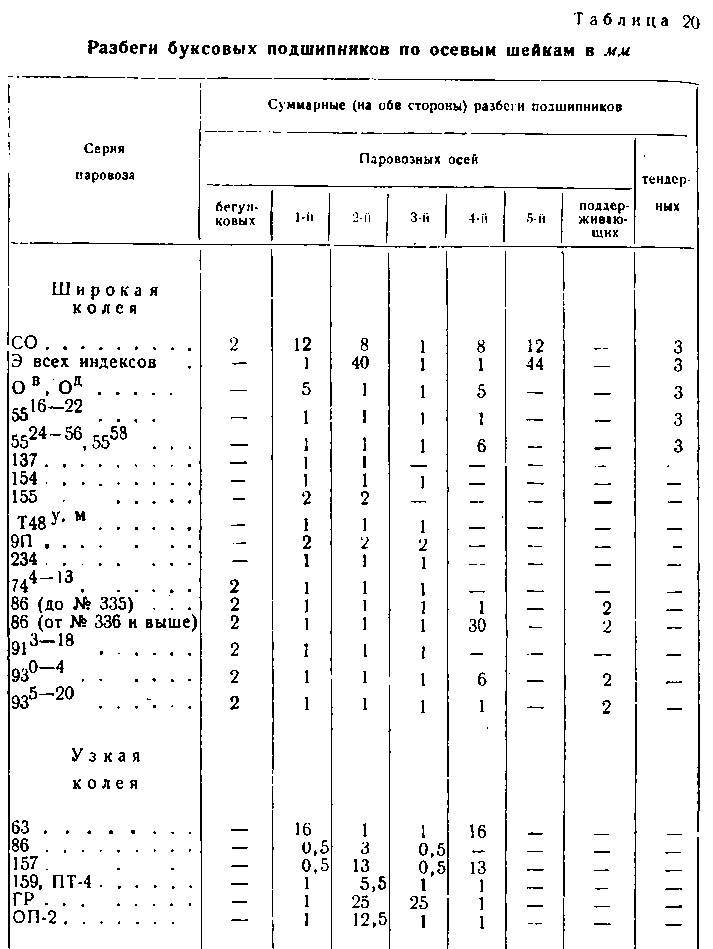
не погнут и правильно пригнан по отверстию. Просевшие клинья нужно сменить или наплавить. Иногда наплавляют подшипники и камни. В период между промывками разрешается пользоваться неукрепленными прокладками при условии изъятия их при очередной промывке котла. При наличии овальности сверх допускаемой стальные втулки необходимо проверить на станке. Ослабевшие втулки, но годные по толщине, разрешается заварить по всей поверхности, приточить и запрессовать вновь.
Натяг дышловых валиков при подъемочном ремонте, необходимо восстановить по чертежным размерам. Валики, кольца и втулки следует цементировать или хромировать. Втулки в хвостовики сцепных дышел следует запрессовывать под давлением 5—8 г; конусы валиков и конусные втулки притирают по проушинам дышел.
Расплавление дышловых подшипников происходит, как правило, из-за небрежного содержания их паровозными бригадами, а именно: из-за недостаточной смазки; чрезмерно тугого крепления подшипников; значительных зазоров в постановке дышловых подшипников, вызывающих стук; выдавливания смазки и нагрева; попадания песка и грязи на шейки кривошипов, а в зимнее время — загустения смазки.
При расплавлении подшипник разбирают, оставшийся баббит выплавляют, заливают новым и растачивают по шейке. После исправления подшипников необходимо проверить с обеих сторон дышло по центрам. Зазоры между подшипником и рамкой устраняют наплавкой меди снаружи подшипника. Подшипники ползунов, а также дышловые втулочные должны работать на бронзе без заливки баббитом. Поршневые и центровые подшипники заливают баббитом. Сцепные и рамочные подшипники могут работать с заливкой и без заливки баббитом.
Периодический осмотр дышел производят, обязательно сняв их с пальцев кривошипов.
После осмотра и определения характера ремонта дышла передаются на сварку, которую выполняют с предварительным подогревом и последующим отжигом ремонтируемых мест.
Разрешается производить следующие сварочные работы: 1) наплавлять изношенные рамки и отверстия под втулочные подшипники, стальные втулки и шарнирные валики; 2) наплавлять боковые грани дышловых головок и места под скобы поршневых дышел; 3) наплавлять изношенные места скобы поршневого дышла; 4) заваривать надрывы в ушках и серьгах сцепных дышел, если надрыв не распространяется глубже 25% живого сечения; 5) наплавлять изношенные места скобы поршневого дышла; 6) при среднем и текущем ремонтах заваривать трещины по масленке сцепных дышел с последующей насадкой хомута, а также наплавлять изношенные поверхности камней ползуна, дышловых вкладышей и скоб; 7) при текущем ремонте наплавлять подшипники по наружным боковым граням и рабочим поверхностям, заваривать не более двух трещин в полшипниках пои условии, что глубина каждой трещины не более
30% живого сечения и наплавлять дышловые заливки (кроме хвостовиков) .
После осмотра и наварки изношенных частей дышла размечают и проверяют, затем производят слесарные и станочные работы.
Ремонт кулисного механизма. Неисправности кулисного механизма заключаются главным образом в износе трущихся поверхностей, заварке валиков, возникновении трещин и обрывов элементов механизма.
В кулисе изнашиваются поверхности скольжения камня, камень, цапфы, подшипники подвешивания, отверстие в ушке захвата кулисы эксцентриковой тяги. Если игра кулисного камня в рамке более 0,2 мм при заводском и 0,25 мм при подъемочном ремонте, трущиеся поверхности рамки шлифуют на специальном станке, а камни заменяют новыми.
Трущиеся части кулисного механизма не должны иметь задиров и забоин. Валики при сборке должны входить в свои места, без принуждения и перекоса. Все кулисные валики и втулки следует цементировать или хромировать.
При ремонте деталей кулисного механизма разрешается восстанавливать наплавкой разработанные отверстия; заваривать трещины в проушинах и вилках, если они не распространяются глубже 25% живого сечения, с усилением заваренных мест наплавкой; сваривать кузнечным способом кулисные тяги, маятники и поводки; восстанавливать наплавкой изношенные поверхности золотниковых кулачков и их параллелей, а также заваривать трещины в кулачках; удлинять и укорачивать подвески золотниковых тяг; удлинять и укорачивать эксцентриковую тягу за счет эксцентричности втулки до
3 мм, а выше — за счет подсадки или протяжки (на длине не менее 500 мм)\ наплавлять изношенные поверхности и заваривать трещины деталей переводного механизма.
При ремонте кулисного механизма паровозов необходимо добиваться минимального отклонения от чертежных размеров элементов механизмов, а также зазоров в шарнирных соединениях, так как с увеличением отклонений увеличиваются погрешности в работе паровой машины, что приводит к перерасходу пара, топлива и воды. Особенно сильно влияют на правильность парораспределения отклонения в длине золотниковой и эксцентриковой тяг и зазоров в шарнирных соединениях золотникового кулачка с маятником, кулисного камня с золотниковой тягой, а также между камнем кулисы и кулисой.
Запрещается заварка трещин в кулисной раме и ее подсадка; заварка трещин по штанге эксцентриковой тяги, а также маятника, кулисной тяги и поводка.
. К неисправностям переводного механизма относятся: износ подшипников, износ резьбы переводного винта и его гайки, а также износ подшипников переводного винта и вала.
Разрешается производить следующие сварочные работы при ремонте переводного механизма: наплавлять отверстия рычагов и места под подшипники вала при износе их не более 15%; заваривать
шпоночные канавки и приваривать новые части вала; наплавлять хвостовики винта (с предварительным подогревом до 300—400°), отверстия для валиков, забоины и изношенные поверхности тяги винта, а также поверхности зубчатого колеса и запорной ручки переводного винта. Тяги перед наплавочными работами рекомендуется подогревать до 300—400°.
ПРОВЕРКА ДВИЖУЩЕГО И ПАРОРАСПРЕДЕЛИТЕЛЬНОГО МЕХАНИЗМОВ
Назначение проверки. Для правильной работы паровой машины паровоза, максимального использования его мощности и экономного расходования топлива необходимо периодически проверять работу парораспределительного механизма паровоза.

При проверке парораспределительного механизма паровоза в первую очередь проверяют соответствие размеров отдельных частей (золотников, золотниковых и эксцентриковых тяг, кулисных подвесок, маятника и т. д.), составляющих парораспределительный механизм, чертежным размерам.
Основные размеры кулисного механизма наиболее распространенных паровозов, работающих в промышленном транспорте СССР, указаны в табл. 21, а схемы механизма — на фиг. 182.
На этой фигуре помещены четыре схемы парораспределительного механизма Вальсхарта, которые, помимо различия в самих элементах парораспределения, отличаются еще друг от друга взаимным
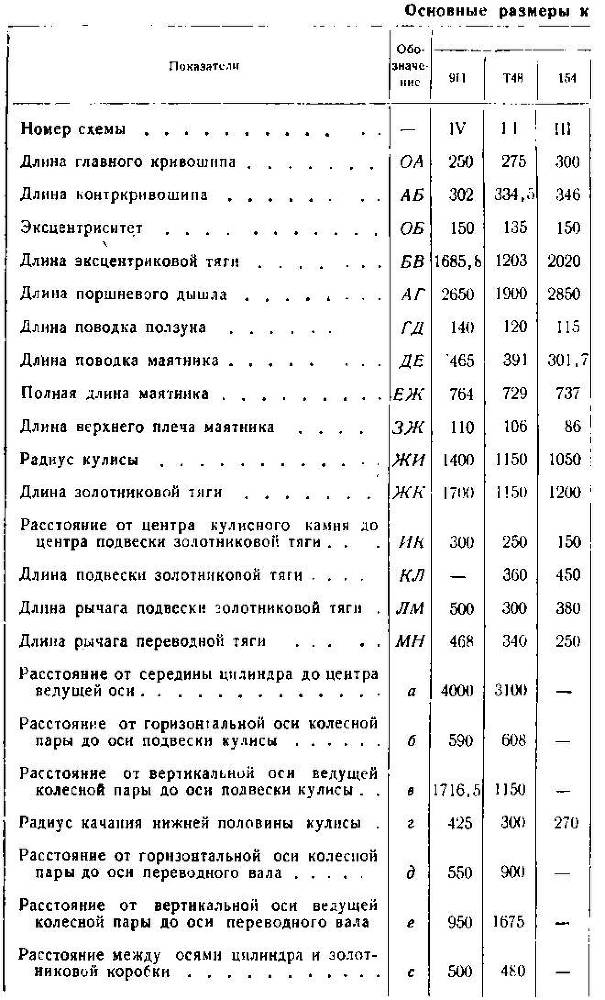
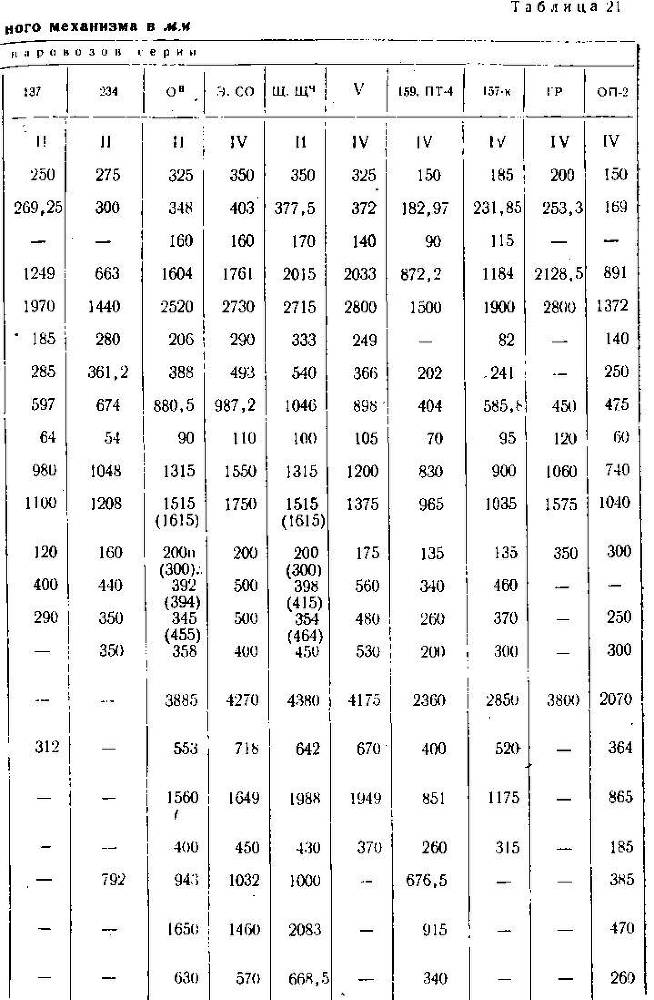
расположением золотниковых скалок и золотниковых тяг; способом подвешивания золотниковых тяг; взаимным расположением контркривошипа и ведущего кривошипа.
После проверки размеров парораспределительного механизма необходима более детальная проверка работы механизма. Полная проверка парораспределительного механизма, т. е. проверка кривошипов, эксцентриковых и золотниковых тяг, подвесок, хода поршней и т. д., как правило, производится при капитальном, среднем и подъемочном ремонтах паровоза. На промывочном ремонте обычно ограничиваются проверкой хода поршней и золотников и только в отдельных случаях, когда обычная проверка хода поршней и золотников к желательным результатам не приводит, производят полную проверку, т. е. проверку всех элементов, влияющих на правильность парораспределения.