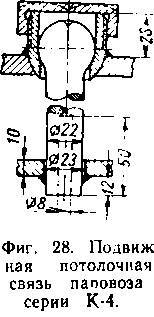
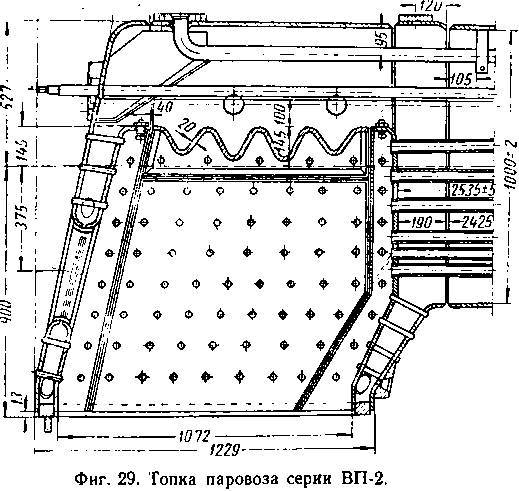
косынками, прикрепленными к листу цилиндрической части. Прежде концы поперечных тяжей ввертывались в лист кожуха. В паровозах последних выпусков тяжи привариваются. Для обеспечения достаточной прочности и жесткости поперечные тяжи делаются из
стали Ст. 2 диаметром 30—35 мм. С обоих концов тяжей имеются контрольные отверстия диаметром 6 мм, глубиной 80 мм.
Углы кожуха с плоским потолком, кроме поперечных тяжей, скрепляют двумя наклонными связями (фиг. 30, д).
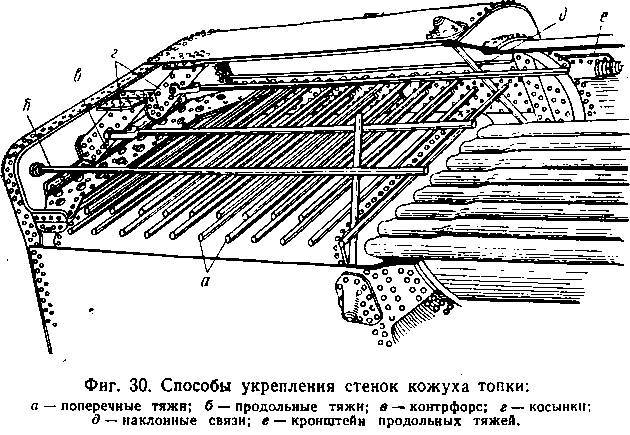
Диаметр средней части наклонной связи 35—40 мм. Верхним и нижним концом наклонная связь ввертывается в фасонные накладки, приклепанные или приваренные снаружи кожуха.
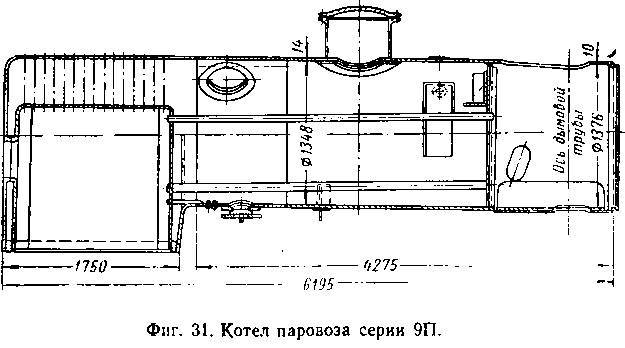
Цилиндрическая часть котла. Цилиндрическая часть котла состоит из 2—4 отдельных барабанов в зависимости от мощности паровоза. Барабаны склепываются или свариваются (фиг. 31),
Количество барабанов для уменьшения соединений берется минимальным; в последнее время котлы промышленных паровозов изготовляются из одного барабана длиной от 1593 до 3258 мм.
Барабаны изготовляются из листовой стали Ст. ЗК толщиной» в зависимости от давления пара и диаметра барабана, 9—18 мм и больше.
Соединение продольных кромок барабана производится двумя или тремя рядами заклепок, причем внутренняя накладка делается шире наружной. Продольные швы располагаются так, чтобы они находились в паровом пространстве, что предохраняет их от разъедания. Кроме того, продольные швы соседних барабанов сделаны вразбивку, что упрощает клепку узлов. Барабаны цилиндрической части котла соединены между собой поперечным швом,
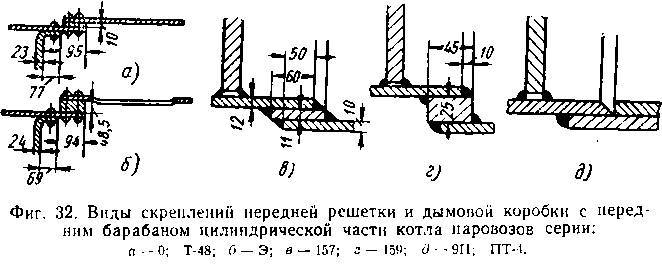
внахлестку, двумя рядами заклепок. В настоящее время котлы паровозов изготовляют цельносварными.
Передняя решетка барабана представляет собой плоскую стенку с отверстиями для установки жаровых и дымогарных труб. Скрепление ее с пе/редним барабаном производится заклепочным швом или приваркой. Решетка (фиг. 32, а, б) имеет отогнутый борт, наружный диаметр которого равен внутреннему диаметру барабана.
Такйе способы укрепления решетки применены на старых паровозах широкой и узкой колеи. На всех новых паровозах передняя решетка приваривается к внутренней части барабана. В этом случае решетка делается из стального листа толщиной от 13 до 25 мм, диаметром на 4—5 мм м’еньше внутреннего барабана (фиг. 32, в, г, д).
Переднюю решетку крепят дымогарными и жаровыми трубами, а выше труб решетку укрепляют контрфорсами различных конструкций (фиг. 33, а, б) — продольными или наклонными тяжами.
Паровой колпак. Для отбора наиболее сухого пара, поступающего в цилиндры паровой машины, на цилиндрической части котла устанавливают паровой колпак. На всех отечественных паровозах паровой колпак устанавливают на цилиндрической части переднего барабана, так как здесь пар при меньшей интенсивности парообразования получается менее влажный. Кроме того, при таком расположе-
нии колпака уменьшается длина парорабочих труб. Размеры паровых колпаков делаются по возможности большими. По мере увеличения размеров котла и повышения его над головкой рельса высота колпаков уменьшается. С уменьшением высоты колпаков диаметр их увели-
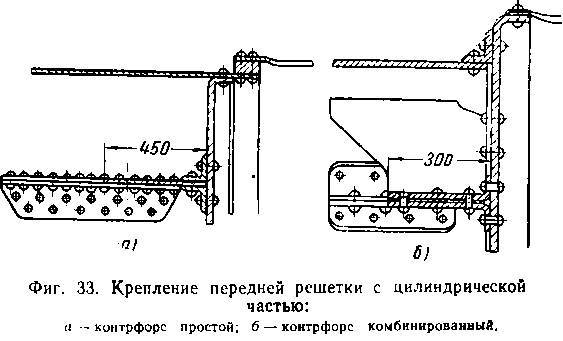
чивается, но увеличение диаметра ограничивается диаметром барабана цилиндрической части котла.
Паровые колпаки делаются разъемными в средней своей части (фиг. 34), клепанными (фиг. 35), сварными (.фиг. 36), с крышкой в верхней части или цельноштампованными.

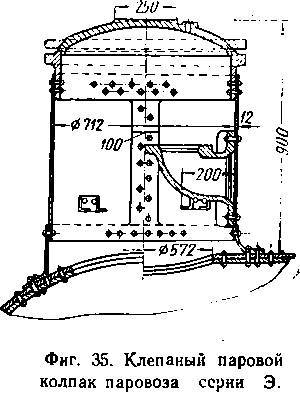
Колпаки закрепляются на котле двумя рядами заклепок или привариваются; при этом для создания большей жесткости некоторые колпаки дополнительно укрепляются к цилиндрической части
котла 6—8 косынками, однако исследования показали, что такое крепление нерационально.
В паровом колпаке располагают регуляторную головку. В цилиндрической части котла для установки колпака вырезается круглое
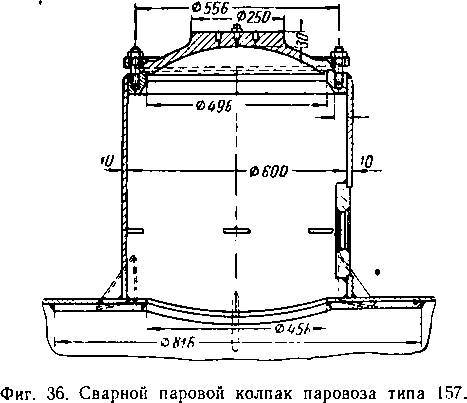
отверстие диаметром от 500 до 800 мм. Для усиления места выреза отверстия с внутренней стороны котла приклепывается или приваривается стальное кольцо толщиной 15—25 мм.
Крышка колпака притирается и прижимается к седлу шпильками. В некоторых случаях применяются прокладные кольца из красной меди.
Колпак и косынки изготовляются из стали Ст. 2, а седло крышки и нажимной кольцо—из стали Ст. 3,
Дымогарные и жаровые трубы. Для лучшего использования тепла и отвода продуктов сгорания из топки паровоза в дымовую коробку и далее в атмосферу паровозный котел снабжен дымогарными и жаровыми трубами (фиг. 37, 38), которые проходят через всю
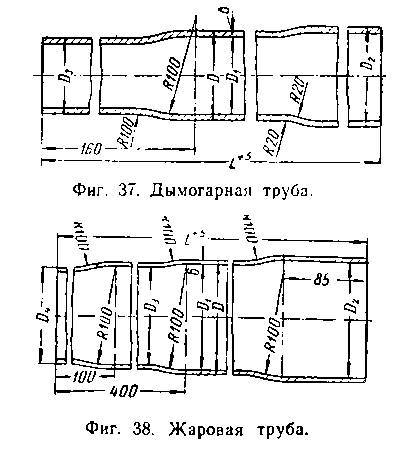
цилиндрическую часть котла и укрепляются концами в задней и передней решетках паровоза.
Жаровые трубы имеют диаметр больший, чем дымогарные. Они служат одновременно для помещения в них элементов пароперегревателя.
Дымогарные и жаровые цельнотянутые трубы изготовляются из мягкой мартеновской стали 10 по ГОСТ 3099-46.
Стандартные формы и размеры дымогарных и жаровых труб паровозов широкой колеи приведены в табл. 6 и 7.
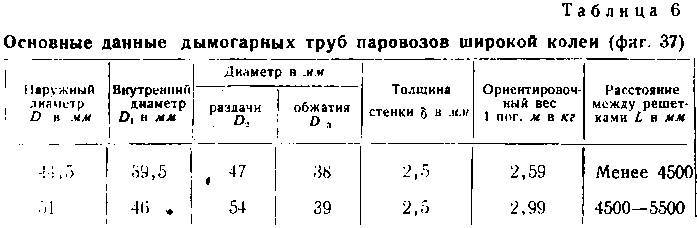
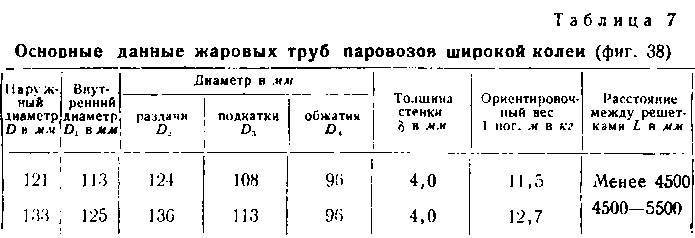
Размещение отверстий для труб в задней и передней решетках должно осуществляться таким образом, чтобы избежать значительного ослабления решеток, сохранить свободный проход пара между трубами и в то же время эффективно использовать площадь решеток.
На современных паровозах дымогарные трубы располагаются по углам ромба, а жаровые — по углам квадрата (Э, СО, .157, 159, ПТ-4) или по углам ромба (ГР, ОП-2) (фиг. 39).
Отверстия для дымогарных труб в новой огневой решетке делаются меньше наружного диаметра трубы, а концы самих труб обсаживаются до этого диаметра для большей прочности огневой решетки и достаточного запаса на рассверливание отверстий при ремонте паровозов.
Передний конец труб, наоборот, раздается для облегчения их выемки. Раздача обыкновенно делается на 3 мм по диаметру как для дымогарных, так и для жаровых труб.
Жаровые трубы, кроме обсадки заднего конца, заходящего в решетку, имеют и другую обсадку, которая делается путем подкатки на расстоянии 250—400 мм от заднего конца трубы. Эта обсадка делается для улучшения прохода пара около верхней части решетки, а также для того, чтобы живое сечение по всей длине трубы было примерно одинаковое, так как в передней части жаровых труб находятся элементы пароперегревателей, уменьшающие живое сечение трубы,
Дымогарные и жаровые трубы ставятся в котел с передней стороны и укредляются в задней решетке с прокладными кольцами из красной меди марки М-4 толщиной 2—3 мм (фиг. 40). Размеры медных колец для установки дымогарных и жаровых труб берутся в зависимости от диаметра отверстия в решетке и ее толщины. Кольцо не должно доходить до огневой поверхности на 0,75—1 мм и выходить в водяное пространство на 2—3 мм.
В настоящей время проводятся опыты постановки труб в заднюю решетку без медных прокладных колец.
Трубы в цилиндрической части располагаются не горизонтально, а веерообразно, с подъемом вперед примерно на 1/100—1/50; такоо расположение труб необходимо для лучшего размещения труб в котле и свободного выхода газов из труб при отсутствии разрежения в дымовой коробке.