Как происходит накатывание резьбы с такой невероятной производительностью?
На вертикально стоящем шпинделе автомата устанавливается закаленный ролик с многозаходной (16- 22 захода) резьбой заданного шага, причем половину диаметра ролика охватывает закаленный сектор с такой же многозаходной резьбой, но нарезанной внутри. Зазор между роликом и сектором может регулироваться и устанавливается равным среднему диаметру резьбы накатываемых винтов. Ролик вращается, сектор стоит на месте. Автомат по непрерывной ленте все время подает из бункера заготовки винтов, и они, попадая в зазор между вращающимся роликом и сектором, непрерывным потоком один за другим прокатываются через установку и сыплются в ящик.
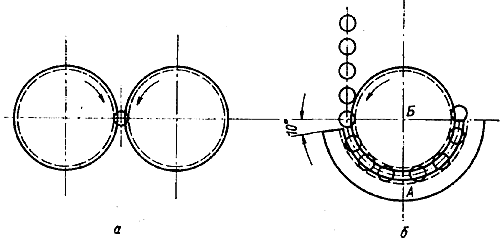
Автомат называется МНК-2. Его производительность поистине удивительна. Ученые из Научно- исследовательского института авиационной технологии (НИАТ) создали специальную машину, на которой методом накатывания изготовляются сразу ролик и заготовка на два сектора. После образования внутренней резьбы круглая заготовка разрезается пополам и половинки закаливаются вместе с роликом. Одна половинка выбрасывается.
Накатывается многозаходная резьба сразу па ролике и секторе специальным длинным мастер-валиком с заданной резьбой. Изготовление мастер-валиков — дело нелегкое даже для очень опытного резьбошлифовщика ввиду их малого диаметра (2-3 мм) и большой длины. На один комплект (ролик — сектор) требуется два мастер-валика. Закаленные ролик и сектор ставят на автомат, и они работают две — четыре смены, после чего резьба на них изнашивается и их выбрасывают.
Наш инструментальный цех был постоянно завален заказами на этот инструмент, так как автомат снабжал крепежными винтами многие родственные заводы, не считая нашего, и его остановка просто не допускалась. На эти секторы и ролики расходовались тонны дорогой легированной стали.
Наша идея заключалась в том, чтобы увеличить долговечность одного комплекта хотя бы в 10 раз. Мы решили вообще отказаться от специальной машины для накатки сектора и ролика. Кстати сказать, эта машина постоянно ломалась и настройка ее требовала долговременной работы квалифицированных слесарей-ремонтников и наладчиков.
16-заходный стальной ролик мы легко нарезали в каленом виде и без специальной машины на универсальном резьбошлифовальном станке. Сектор же с внутренней 18-заходной резьбой мы решили сделать твердосплавным, причем обе резьбы (наружную и внутреннюю) после резьбошлифования довести чугунными притирами, как доводят резьбовые калибры.
С роликом все было просто, даже проще, чем на спецмашине, и качество его было отличным. А вот с твердосплавным сектором… Выяснилось, что еще никто в стране не шлифовал внутреннюю многозаходную резьбу на твердом сплаве.
— А не бросить ли нам это дело? — сказал я как-то Михаилу Васильевичу. — Ведь мы даже не знаем, как это делается, и никто нам не подскажет ничего.
Давыдов подумал с минуту, как бы взвешивая мое предложение, потом твердо заявил:
— Бросать нельзя, надо ехать в Киев к Бакулю, там в институте не такие проблемы решали, помогут решить и эту.
Цеховое руководство усмотрело в нашей идее здравый смысл, поэтому без особого труда я получил командировку к Бакулю. И вот я снова в Институте сверхтвердых материалов.
Валентин Николаевич принял меня очень радушно, внимательно выслушал и просмотрел все, что я привез с собой. Нашу идею он быстро понял и нашел ее хоть и очень смелой, но осуществимой. Нужен был алмазный круг диаметром 30 мм и с углом 60° на такой связке, которая позволила бы при шлифовании резьбы на твердосплавной заготовке сохранить острие круга без осыпания и притупления на протяжении обработки всех 18 заходов.
Таких алмазных кругов Институт сверхтвердых материалов еще не выпускал. Однако Бакуль приказал принять наш заказ и поручил одной из лабораторий института изготовить такие круги в возможно короткий срок. Ученые и инженеры — сотрудники лаборатории очень помогли мне советами, расчетами режимов алмазного внутреннего резьбошлифования и, что не менее важно, своим доброжелательным отношением. Так союз науки и труда помогал проникнуть в неведомое, сделать работу, еще никогда не выполнявшуюся никем. Творческое содружество победило.
Шлифовать 18-заходную резьбу на твердосплавном секторе я решил 21 апреля 1973 г., в день коммунистического субботника, затратив на это одну смену. Я волновался примерно так же, как 35 лет назад, когда 22-летний юнец решил сдавать пробу на 7-й разряд на заводе «Пневматика» в Ленинграде. Конечно, сейчас я чувствовал себя уверенней. Тогда у меня были бесценные советы моего дорогого учителя Павла Алексеевича Шведова, а теперь кроме собственного немалого опыта со мной была наука, а это очень много значит!
И в этот раз на заводе было немало скептиков и просто любопытных, недоверчиво посматривавших на мой токарный станок, который я переоборудовал на внутреннее алмазное резьбошлифование. Но все прошло почти без запинки. Станок имел необычный вид. Чтобы алмазный круг до острия прорезал каждый заход внутри твердосплавной заготовки, нужна скорость резания 45 метров в секунду, а для этого алмазный круг должен вращаться со скоростью 60 тысяч оборотов в минуту. Такую скорость мне удалось получить, приспособив к своему станку «фортуну». Алмазным кругом я нарезал сектор как полный круг, а после разрезки прорезным алмазным кругом получил два полноценных сектора. Теперь выбрасывать вторую половинку не было причин.
Результат наших исканий превзошел все ожидания еще в 10 раз: сделанный нами сектор проработал на автомате МНК-2 полгода вместо четырех смен и дал 12 миллионов винтов вместо обычных 200 тысяч.
Стальных роликов потребовалось в 4 раза меньше, чем их расходовалось в паре с обычным стальным сектором; видимо, резьба твердосплавного сектора выправляла износ резьбы стального ролика, и тот работал теперь значительно дольше.
Вот какой эффект дает союз науки и труда, союз, о котором так правильно говорил Валентин Николаевич Бакуль! Он попросил меня написать статью об этой работе в журнал Института сверхтвердых материалов «Синтетические алмазы». Статья была напечатана в № 5 за 1973 г.
…Из последних творческих поездок хочется отметить командировку в Саратов. Поехал я туда по настойчивым и неоднократным приглашениям ряда заводов и Саратовского областного общества «Знание».
Стояла зима 1974 г., в городе было много снега. Волга, которая под Саратовом очень широка, покрыта толстым льдом. На другом берегу находится город Энгельс. Соединяет оба города самый длинный в Европе мост необычной, волнообразной конструкции. Мне пришлось несколько раз проезжать по этому мосту, чтобы посетить некоторые заводы в Энгельсе для оказания технической помощи.
Вместе со мной в Саратов был приглашен еще один московский новатор, очень интересный человек — слесарь-механик Андрей Кузьмич Семенов. Тема, ради освещения которой его вызвали саратовские институты и заводы, не совсем обычная — скоростное черчение.
На общегородском семинаре специалистов многих заводов и институтов, организованном городским советом ВОИР, обществом «Знание» и Саратовским советом новаторов, Семенов начал свой рассказ так:
— По статистическим данным, за последние 80 лет производительность труда токаря возросла в 20 раз, а производительность труда конструктора и чертежника только на 20%- Вы сейчас рисуете свои чертежи так же, как это делали ваши предшественники еще в прошлом веке. С этим нельзя мириться. Вот я вам сейчас покажу несложные приборы, с помощью которых любой конструктор или чертежник будет «выдавать» свои чертежи в 2,5 раза быстрее, чем это делается везде.