Руководили этими работами высококвалифицированные станкостроители, и в их числе те самые эксперты и рецензенты, которые не сразу сумели за несовершенствами первого предложения разглядеть скрытую в нем прогрессивную идею.
Этот станок совершенно не похож на первый макет. Он оснащен специальными электрическими шаговыми двигателями, способными выполнять сотни шаговых поворотов в секунду. Вся его конструкция продумана и рассчитана на автоматическое действие, устранены люфты и зазоры, к минимуму сведено трение во всех подвижных сочленениях, электронный узел управления обеспечивает высокую скорость расшифровки и передачи шаговым двигателям управляющих сигналов, а программа работы записана очень плотно невидимыми «штрихами» на магнитной ленте.
Но одно в нем осталось от первого макета неизменным — шаговый принцип действия, принцип, позволивший построить станок по простейшей разомкнутой схеме, исключившей необходимость иметь цепь обратной связи, хотя между задатчиком программы — лентой — и исполнительным механизмом — шаговым двигателем — нет жесткой кинематической передачи.
Создание шаговой системы цифрового управления — лишь небольшой эпизод в истории новых идей и техники цифрового управления станками. Но ведь каждая новая глава в истории техники всегда слагается из отдельных эпизодов, и автор выбрал для рассказа тот из них, который ему знаком в мельчайших подробностях.
К тому времени, когда был построен первый макет шаговой системы управления, над созданием станков с цифровым управлением работали ряд организаций в Советском Союзе и бесчисленное множество фирм за рубежом. Сначала единицами, затем десятками, и к сегодняшнему дню уже сотнями насчитываются различные системы цифрового управления станками — фрезерными, токарными, координатно-расточными, сверлильными, специального назначения. Построены они как по разомкнутой схеме — с использованием шаговых двигателей, так и по замкнутой схеме с цепью обратной связи.
Чем объяснить такой бурный разворот? Так ли уж нужны эти станки? Вот один пример.
Корпус современного самолета состоит из крупных монолитных деталей фасонной конфигурации, благодаря чему фюзеляж и крылья имеют такую изящную обтекаемую форму. Размеры этих деталей достигают иногда 20 метров в длину, причем для обработки некоторых из них методом копирования необходим комплект из трех различных копиров.
Одной из зарубежных самолетостроительных фирм подсчитано, что для обработки всех деталей корпуса тяжелого самолета нужно немногим меньше 2 тысяч копиров. Заготовки, которые будут обрабатываться по этим копирам, а также заготовки других деталей предварительно штампуются в специальных штампах. Таких штампов требуется 3–5 тысяч штук.
Помимо этого, при подготовке к производству каждого нового типа самолета требуется значительное количество шаблонов, которые служат для контроля при изготовлении самых различных деталей самолета. И если по каждому из копиров и штампов в дальнейшем будут изготовлено не одно, а несколько изделий и заготовок, в зависимости от количества выпускаемых, самолетов данного образца, то шаблоны, как правило, изготовляются всего лишь в одном-двух экземплярах. На один тип самолета обычно требуется 15–20 тысяч шаблонов.
Наконец, при наладке металлорежущих станков, ведущих обработку прочих деталей тяжелого самолета, требуется до 1000 различных кулачков. Время, которое необходимо только на обработку криволинейных профилей и поверхностей всей так называемой оснастки (штампов, копиров, кулачков, шаблонов), исчисляется сотнями тысяч часов и связано с затратой очень больших средств. А конструкции самолетов изменяются, как мы знаем, часто. При переходе к выпуску новой модели всю эту работу приходится начинать заново. И если не обеспечить высокий темп производства, то новый самолет окажется устаревшим еще до того, как кончится изготовление нужной для его производства оснастки.
Точно так же обстоит дело со многими деталями ракет и газовых турбин, современных приборов и радиоаппаратуры. Вот почему ученые и инженеры вынуждены искать решения, которые позволили бы автоматизировать процессы обработки деталей без изготовления копиров или специальных механизмов. Другими словами, не моделируя физическими средствами ту программу, по которой должен работать автомат.
И постепенно станки с цифровым управлением получают прописку в цехах заводов. Сначала это нежелательные жильцы — ведь они требуют повышенной заботы, пристального внимания и особого ухода. Они сложны по конструкции, густо оснащены электроникой. Они не наилучшим образом приспособлены к жизни в цеховых условиях.
А главное (самое главное!) — ведь раньше обходились без них. Значит, и в дальнейшем можно обойтись.
Но вот к новоселу присмотрелись, приноровились и наладили его для обработки самой сложной детали, на изготовлении которой всегда спотыкались в цехе. И вот тут новичок показал, на что он способен: в одну смену он изготовил столько деталей, сколько раньше цех не изготавливал за неделю.
К этому времени были рассчитаны программы на обработку трех других изделий, вызывавших крайнее неудовольствие технологов своей сложностью. И станок, не остыв от обработки одного изделия, уже начал обрабатывать вторые, третьи, четвертые.
Теперь уже не надо было для каждого из этих изделий заказывать в инструментальном цехе копиры, требуя, чтобы они были тщательно изготовлены с высокой точностью и из высококачественных материалов. Не надо было ломать голову над проектированием специальных механизмов, которые могли бы обеспечить то или иное движение инструмента относительно заготовки — разное для разных изделий.
Почти ничего не надо было менять в станке для того, чтобы заставить его вместо одного изделия обрабатывать совершенно другое. Из вычислительного центра в цех приносили магнитную ленту, на которой была записана программа обработки нового изделия. Ее устанавливали на пульте управления, включали станок, и он принимался за обработку нового изделия.
И если в действительности эта картина выглядела далеко не так просто, как мы сейчас рассказали, то тем не менее решение приспособить числа для управления станками было хорошей догадкой, было полноценным изобретением. Пусть вначале несовершенное и опробованное лишь в самых грубых макетах — оно содержало рациональное зерно. Это зерно не могло не быть замечено и скоро начало давать ростки, а затем и плоды — станки, построенные с использованием новых идей. Показав себя в деле с лучшей стороны, они из нежданных и непрошеных гостей вскоре становятся самыми желанными.
Сначала единицы, затем десятки, сотни, а теперь тысячи станков с цифровым управлением трудятся в цехах заводов. Появляются все новые и новые автоматы и целые автоматические линии с цифровым или, как обычно говорят, с программным управлением. На этажерке современных автоматов они располагаются почти на самых высоких полках.
Но и у этих автоматов, как и у всех других, есть свои «предки». О них пойдет рассказ в следующей главе. Он будет тем более полезен, что многие из этих «предков» до сегодняшнего дня честно и самоотверженно работают на благо человеку и, наверное, все так же будут работать не один десяток лет.
«Абстрактная» картина, «конкретная» мелодия
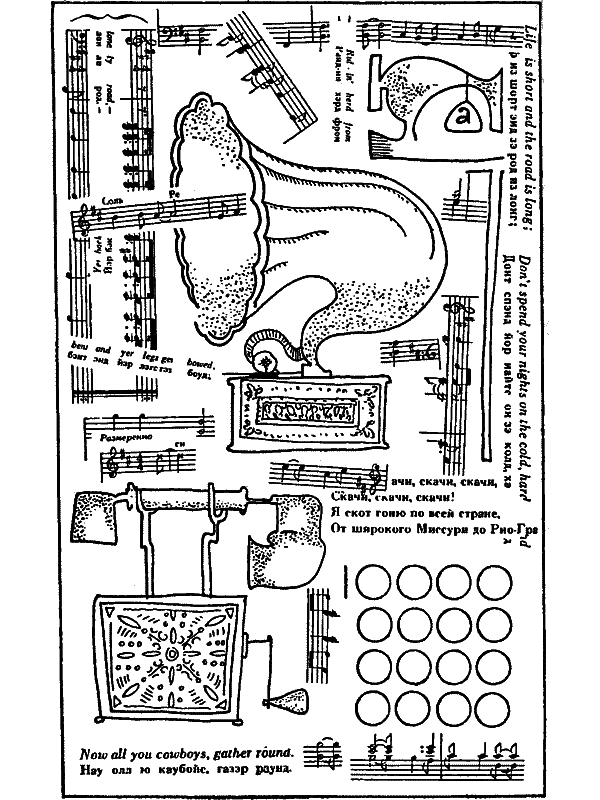
В 1801 году на промышленной выставке в Париже среди прочих экспонатов был выставлен ткацкий станок, вокруг которого всегда толпились посетители. Этот станок был оборудован устройством, механизировавшим самую сложную часть процесса выработки узорчатой шелковой ткани, ранее требовавшую большого искусства и напряженного труда двух-трех ткачей.
Изобретателем этого станка был француз Джозеф Жаккар. Сын лионского ткача, он еще в юности, работая ткачом, предпринял попытки усовершенствовать свое орудие производства.
Путь Жаккара не был, как говорят, усеян розами. Достаточно сказать, что один из первых образцов созданного им станка был уничтожен его земляками — лионскими ткачами, боявшимися, что это изобретение лишит их куска хлеба. Однако он продолжал работу. Длилась она с перерывами около тридцати лет, пока, наконец, ему удалось добиться своего.