Поскольку во всех существующих неавтоматизированных системах управления идея оптимизации (выбора наилучшего варианта) полностью игнорируется, то, автоматизируя составления межцехового плана, приходится чуть ли не заново создавать всю систему. Что же можно улучшить, вооружившись ЭВМ и используя экономико-математические методы при планировании?
Во-первых, вполне возможно значительно увеличить подробность планирования, хотя и не до уровня отдельных операций, которые являются объектом внутрицехового планирования, планировать более мелкие этапы изготовления изделий, настолько мелкие, насколько это необходимо для данных конкретных условий управления.
Во-вторых, можно значительно точнее учитывать связи между этапами изготовления и очередность их выполнения. Традиционный подход к планированию предполагает последовательное выполнение этапов. В реальном же производстве часть их всегда осуществляется параллельно. Необязательно, например, сначала отливать все заготовки деталей, а потом изготавливать все детали. Заготовок можно сделать лишь часть, а остальные делать параллельно с изготовлением деталей из уже имеющихся. На языке календарного планирования это означает, что этапы изготовления изделия увязаны между собой в сетевой график, который значительно правильнее отражает производственный процесс, а следовательно, способствует более успешному планированию.
В-третьих, экономико-математические методы предполагают наличие в своем арсенале алгоритмов взаимной увязки сетевых графиков изготовления всех изделий с учетом ограничения по ресурсам и с оптимизацией по необходимому критерию. В результате применения такого алгоритма получается оптимальный межцеховой календарный план.
Полученный таким путем план может рассматриваться с двух точек зрения, или, как говорят в производстве, в двух разрезах. С одной стороны, это и будет межцеховой календарный план, который необходим руководителям предприятия для координации работы цехов и контроля за процессом изготовления изделия. С другой стороны, на базе его можно составить перечень того, что каждый цех должен делать каждый месяц, то есть будет составлена производственная программа цеха на месяц. Заметим, что она при этом будет уже сбалансирована с мощностью цеха.
— Теперь, когда методы автоматизации разработаны, разнобой в системах планирования, по-видимому, кончился?
— Кончился бы, если бы в производстве не действовал еще один фактор, существенно влияющий на стройность этих систем.
— Кажется, учтено уже все?
— Вы забыли, наверное, что в формуле АСУ есть слагаемое «плюс организация»!
Каждые 22 секунды с главного конвейера Волжского автозавода сходит новенький, сверкающий автомобиль «Жигули». Это значит, что каждые 22 секунды к главному конвейеру должен быть подан комплект деталей — несколько тысяч разнообразных «кусочков» этого автомобиля, от кузова до винтика. Своим ритмом — 22 секунды — главный конвейер задает ритм жизни всему предприятию. Как крупная река питается притоками, так и главный конвейер по ходу движения «подпитывается» вспомогательными конвейерами и поточными линиями. Ритм каждого конвейера, каждой поточной линии, каждого рабочего места равен или кратен 22 секундам, как говорят, согласован с ритмом главного конвейера.
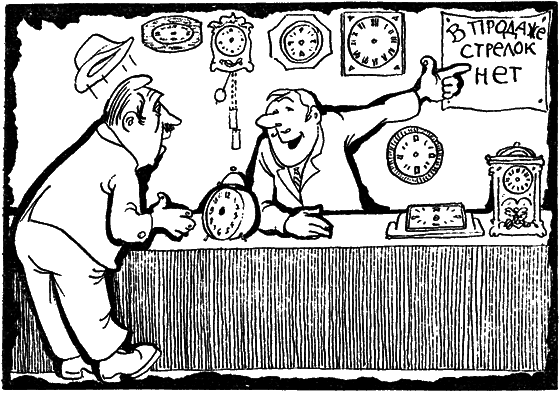
Рабочие места в поточных линиях максимально специализированы. Каждый рабочий выполняет одну операцию на специально предназначенном для этой цели оборудовании. При этом им достигается максимальная производительность труда, наилучшее использование материалов.
Так налажено массовое производство — 660 тысяч автомобилей в год.
Это, безусловно, самый совершенный тип производства. Совершенство это объясняется тем, что практически любые затраты на усовершенствование его организации окупаются. В самом деле, если обнаружена возможность сократить трудоемкость операции на одну минуту, то этой возможностью надо немедленно воспользоваться, так как она дает годовую экономию в 660 тысяч минут, то есть 11 тысяч часов в год рабочего времени. Если предложен новый технологический процесс, внедрение которого экономит на изготовлении детали 100 граммов металла, то его, безусловно, надо внедрять, так как это приведет к годовой экономии в 66 тонн. Вот почему уже при проектировании завода массового производства конструкторы и технологи до мелочей продумывают не только конструкцию изделия и технологический процесс изготовления его, но и расположение оборудования, согласование ритмов работы всех рабочих мест, в общем, все, вплоть до рациональных движений рабочего. Планирование такого массового производства предельно простое: каждые 22 секунды… и т. д.
Массовое производство — это идеал организации, управления и экономичности, это мечта каждого, кто занят в управлении производством. К сожалению, идеалов очень мало и не на всех хватает. Кроме того, не все изделия промышленности нужны народному хозяйству в количестве 660 тысяч штук в год. Так, средних токарных станков достаточно примерно 12 тысяч штук в год. В этом случае создавать главный сборочный конвейер с ритмом выпуска в 20 минут (такой ритм обеспечивает выпуск 12 тысяч станков в год, 50 штук в день), в общем, нецелесообразно. 50 станков в день можно собрать и непосредственно в сборочном цехе, не затрачивая средства на установку конвейера с дорогостоящим оборудованием. Делается это так.
Бригада сборщиков начинает монтировать несколько станков сразу и доводит монтаж до конца. Естественно, что для этого нужны детали и узлы станков. Механические цехи и цехи узловой сборки должны поставлять в день 50 комплектов этих деталей. Изготовление их тоже ведется не так, как в массовом производстве: здесь одной операцией рабочего не загрузишь, 12 тысяч деталей он может обработать меньше чем за месяц, а что ему делать в оставшиеся месяцы? Переходить к другой операции? В этом случае теряется преимущество узкой специализации рабочего — он должен учиться делать эти другие операции, которых может быть десяток, иногда несколько десятков.
Можно организовать работу, конечно, и так: рабочий обработал сначала 12 тысяч одних деталей, потом 12 тысяч других и т. д. Абсурд такой организации очевиден. Последняя деталь при таком управлении появится лишь в конце года, и все ранее изготовленные изделия должны лежать и ждать эту деталь. А ведь на сборку каждый день должно прибывать 50 комплектов!
Вот почему изготовление 12 тысяч деталей расчленяется на куски — партии. Каждый рабочий в течения какого-то времени обрабатывает сначала партию одних деталей, потом других, третьих и т. д. Потом цикл начинается снова. Все детали сдаются на склад, который и выдает на сборку по 50 комплектов в день и следит за комплектностью своих запасов.
Выпуск станков, как уже замечено, тоже осуществляется партиями. Их еще называют сериями, за что все производство получило название серийного.
Конечно, серийное производство менее эффективно, чем массовое. Во-первых, из-за оборудования: оно должно быть универсальным, то есть настраиваться и переналаживаться на десяток различных операций, а универсальное оборудование менее эффективно, чем узкоспециализированное, рассчитанное на массовое производство. Во-вторых, при переходе от одной операции к другой производительность труда рабочего падает: он ведь тоже «переналаживается». Можно добавить и «в-третьих» и «в-четвертых».
Но серийное производство тем не менее существует по объективным причинам и, несмотря на меньшую эффективность по сравнению с массовым, наверняка будет существовать и впредь.
Планирование в серийном производстве в основном сводится к двум элементам. Первый — это определение оптимальных размеров партий обрабатываемых деталей, собираемых узлов и станков. То, что эта задача непростая, видно из следующих соображений. С одной стороны, «чем больше, тем лучше»: увеличение размеров партии благоприятно сказывается на увеличении производительности труда (рабочие привыкают) и на сокращении времени переналадок. С другой стороны, «чем меньше, тем лучше»: большие партии деталей занимают много места для хранения, что увеличивает затраты и «замораживает» много материала и труда — все это лежит без пользы. Вот и приходится выбирать некоторое среднее решение — оптимальный размер партии.