Перед загрузкой в башню трава измельчается на кусочки порядка 1–2 сантиметра, после чего забрасывается пневматическим транспортером наверх. Постепенно заполняя башню, она уплотняется под собственной тяжестью и внизу буквально спрессовывается. Поэтому для выгрузки ее через нижние люки делаются специальные пилящие и выскребывающие устройства.
Биохимические процессы, протекающие в герметически закрытой сенажной башне, очень сходны с вышеописанными, однако молочнокислое брожение здесь заканчивается раньше. Чтобы прекратить процессы гниения «в самом зародыше», башни полезно заполнять инертным газом, например углекислым. Потери корма в таком случае не превысят 15 процентов. Кстати, аналогичный результат можно получить и простой упаковкой сенажа в полиэтиленовый герметичный мешок. Так иногда и делают, хотя расходы на мешки (делают их громадными — на несколько тонн травы сразу) за несколько лет становятся вполне сопоставимыми с расходами на строительство башни.
В последние десять лет при закладке травы на сено, силос или сенаж стали использовать различные химические консерванты, биохимические закваски и даже ионизирующие облучения. Все это позволяет очень существенно снизить потери и улучшить качество корма. Но никак не приводит к уничтожению одного из существеннейших недостатков…
И сено, и силос, и сенаж в готовом к употреблению виде — рыхлая масса. После того как ее вытащили на воздух, ее следует немедленно употребить в дело (известно, что открытые консервы портятся быстрее, чем свежие продукты). Поэтому все хранилища для этих видов кормов строятся вблизи места скармливания — на соседнюю ферму, а тем более взаймы соседу этот корм не отвезешь. Кроме того, силос из наиболее молодых, ценных в питательном отношении растений обычно получается плохой, животные едят его без особого удовольствия: запах от него исходит не слишком аппетитный, а сладости мало; все-таки брожение есть брожение.
Способ борьбы с нетранспортабельностью рыхлой растительной массы и вызванными этим потерями при перевозках и раздаче корма найден уже довольно давно. Примерно сто лет назад на полях появились первые прессы, позволяющие превращать рассыпчатую солому и сено в плотные тюки. Технология сенопрессования несложна: вначале та же косилка и грабли, затем подборщик. Механизмы последнего отправляют подсохшее сено в прессовальную камеру, где движется поршень… Спрессованный тюк перевязывают шпагатом или проволокой и перевозят к месту складирования. Перевязывать тюк приходится обязательно: растительная масса — материал слишком упругий и склонный восстанавливать свои размеры после снятия нагрузки.
Наличие вязального аппарата на пресс-подборщике усложняет конструкцию машины. Да и расход перевязочных средств ощутим, попадание же в корм кусков металлической проволоки (если тюк связывают ею) — явление тоже не слишком желательное. Избежать всего этого можно, значительно уменьшив размеры тюка и увеличив рабочее давление в прессовальной камере. Если сено как следует сжать, то расправиться оно уже не сможет. Этот принцип используется в конструкции пресса-брикетировщика. Его продукция — плотные небольшие брикеты. Обходятся они, однако, дороже обычного тюка: слишком много нужно энергии для сильного сжатия массы.
Но главное все-таки не в высокой стоимости прессованного сена. Главное — в необходимости провяливания, просушивания травы в неустойчивых полевых условиях. А чем больше операций в поле, тем больше потери, больше наша зависимость от погодных условий, меньше возможности сделать кормопроизводство промышленным. При заготовке сенажа и силоса относительно низко и качество корма, так как потери витаминных комплексов очень велики. Витамины же очень нужны. Это обстоятельство неопровержимо доказал еще в 1906–1912 годах английский биохимик Гопкинс. Он составлял самые высококалорийные питательные смеси из очищенных белков, жиров, углеводов и минеральных солей, кормил ими мышей и всякий раз убеждался в том, что более четырех недель они подобного откорма не выдерживают. Помирают.
— А почему, собственно, необходимо сушить траву? Почему бы сразу не забрикетировать весь луг?
— Если бы это было возможно! Брикеты из свежескошенной травы получаются превосходными. Беда лишь в том, что они так быстро и интенсивно покрываются плесенью, что животные отказываются даже смотреть на них.
— Но, может быть, брикеты можно сушить?
— При сушке брикетов наступает «эффект бревна» — сушатся только наружные слои, внутренние остаются влажными. В итоге опять плесень.
Эффекта бревна избежать не удается. А вот обойтись без него можно. Для этого надо сразу же после того, как трава скошена, пропустить ее через раскаленную сушильную печь: при температуре порядка 350–600 градусов сушка травы сопровождается лишь незначительным «выгоранием» каротина. Получаемый таким способом продукт принято называть витаминной травяной мукой (мукой потому, что после сушки трава перемалывается до порошкообразного состояния).
Травяная мука — отличная белковая добавка в рацион всех животных и птиц. Есть, однако, и в этом процессе свои минусы. Во-первых, при хранении муки происходит интенсивное окисление ее и содержание каротина очень быстро падает. Во-вторых, при раздаче пылевидного сухого корма очень много его теряется: он липнет к стенкам кормушек, к деталям транспортеров, на него просто опасно дышать — хорошо, что коровы чихать не умеют.
С потерями при хранении травяной муки ведут борьбу либо упомянутым уже помещением ее в среду инертных газов, либо путем прибавления к муке специальных химических веществ — антиокислителей. Получается неплохо, хотя и дороговато. Что же касается второго минуса, то его легко превратить в плюс, пропустив травяную муку через пресс-гранулятор. Эта машина делает из муки небольшие гранулы, напоминающие конфеты-батончики. Такой корм легко транспортировать, хранить, он легкосыпуч, не зависает на стенках бункеров и хранилищ, а главное — с аппетитом поедается. Помимо всего прочего, в гранулы можно добавлять и другие компоненты — например, перемолотое зерно, дробленую солому, минеральные соли — в зависимости от вкусов животных и рекомендуемой диеты. Получается комбинированный корм…
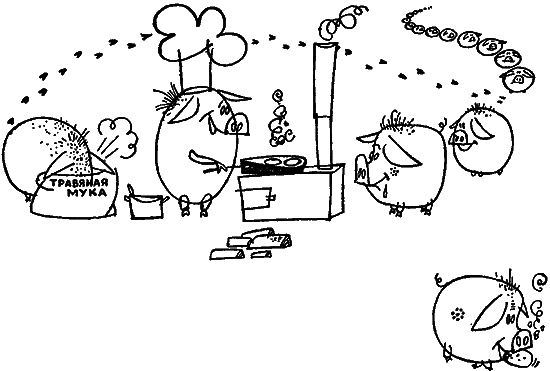
Комбикорма известны уже более ста лет. Сейчас они изготавливаются по самым разнообразным рецептам на крупных комбикормовых заводах и составляются зачастую из сотен различных компонентов. В их число входят не только различные виды зерновых культур, но различные отходы растительного и животного происхождения, отходы свеклосахарных и других пищевых предприятий. Обязательными добавками, вводимыми в комбикорм, являются так называемые премиксы — обогатительные смеси из белковых веществ, витаминов, макро- и микроэлементов, антибиотиков.
Комбикормовые современные заводы — очень крупные автоматизированные предприятия. Основную часть исходных продуктов им поставляет сельскохозяйственное производство. Таким образом, здесь мы имеем дело с встречными потоками: туда — зерно и некоторые другие продукты, сюда — комбикорм.
В последние десять лет у нас начали строить много районных комбикормовых цехов. К сожалению, районы в стране далеко не одинаковые по размерам: где-нибудь в густонаселенной Украине район может быть невелик, в Казахстане же и Сибири — занимать площадь больше, чем иное европейское государство. Естественно, что и подход к строительству заводов должен быть здесь разный. В противном случае гигантомания может привести к тому, что транспортные издержки (на встречные перевозки) подпрыгнут до 70 процентов стоимости комбикорма!
Очевидно, что нам нужны разные заводы: и большие, межколхозные, и колхозные — все решает конкретная обстановка, экономика…
Итак, мы заканчиваем наш разговор о проблемах кормления домашних животных, волею судеб и технического прогресса навсегда оторванных от родной природы и заточенных внутрь бетонированных каменных мешков. Теперь мы ежегодно выгоняем на наши поля не стада, а машины, которые косят, возят, измельчают, сгребают, прессуют, дробят и перетирают миллионы тонн корма. Вслед за тем значительная часть собранного попадает в город, на комбикормовый завод, где все вновь мелется, дробится и смешивается…