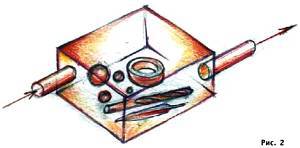
Затем ящики ставили в электропечь. В каждый из них через отверстия непрерывно продували аммиак. При температуре около 700 °C аммиак медленно отдавал свой азот поверхностному слою металла. Процесс длился от двух до девяноста часов. В последнем случае азотом успевал пропитаться слой толщиною до 0,8 мм. Здесь он частично вступал в соединение с атомами железа, а часть его оставалась в состоянии твердого раствора. Именно ионы азота в железе и придают металлу особую прочность. Увеличение же содержания азотистых соединений делает его хрупким.
Тут прервем наш рассказ и поговорим о прочности материалов вообще. Часто думают, что она вызвана силами молекулярного притяжения. Это верно, но лишь отчасти. Расчеты показывают, что если бы это было так, то все материалы были бы в тысячи раз прочнее, чем мы наблюдаем. Оказывается, во всех материалах действует еще и процесс образования дефектов кристаллической решетки. На них собираются и концентрируются в очень малом объеме любые силы, приложенные к материалу. С этих-то мест — их называют местами концентрации напряжения — и начинается разрушение.
Попробуйте намотать на руки и разорвать на две части обычный полиэтиленовый пакет. Это нелегко! Однако стоит проткнуть его ножом, и он мгновенно разорвется по дырке.
Однажды ученые определили предел прочности кристалла каменной соли на разрыв. Получилось 200 кг на квадратный миллиметр — как у очень хорошей стали! Почему же мы обычно такой прочности у соли не наблюдаем? Причина проста. Все дело в дефектах структуры.
Все виды упрочняющей обработки любых материалов, по крайней мере, частично сводятся к устранению существующих в них дефектов. Их прекрасно «залечивают» растворенные в железе ионы азота. Но нитраты, соединения азота с железом, хоть они и сами по себе очень прочны, способны создавать новые дефекты. Потому процесс азотирования хорош в меру. И хотя азотированию поддаются многие сорта стали, у тех, что содержат алюминий, оно происходит особенно успешно: образуется твердый слой, который царапает стекло и может быть обработан только алмазом. Когда дагестанский кузнец закапывал проволоку в пропитанную мочой животных землю скотного сарая, он тем самым создавал условия для образования на ней азотно-аммиачных соединений. Напомним, что эту проволоку скручивали с проволокой, висевшей на солнце. После многократного разогрева и ковки азотистые соединения разлагались, и в заготовке кинжала возникал твердый раствор азота, придававший металлу упругость и твердость.
Сегодня производство холодного оружия отошло далеко на задний план, а азотирование широчайшим образом применяется во всех отраслях техники. Азотированную поверхность имеют рабочие поверхности измерительных инструментов, например, штангенциркулей или микрометров. Азотируют также трущиеся участки поверхности осей и валов. Особенно этот процесс важен для шестерен. Азотированная поверхность не только снижает их износ, но и уменьшает силу трения зубцов шестерней. Механизмы становятся гораздо надежней и экономичней.
Не избежали применения азотирования и металлорежущие инструменты — фрезы, резцы, сверла. Но здесь условия работы поверхностного слоя особенно тяжелы.
На кромке резца токарного станка напряжение достигает предела прочности материала, температура может приближаться к 1000 °C. Плотность проходящего через нее потока энергии не ниже, чем у лазера противоракетной обороны. Для защиты кромки резца от разрушения на нее напаивают пластинки сверхтвердого вольфрамового сплава. Но это не самое хорошее решение. Такой сплав очень тверд, стоек к износу и в то же время хрупок. Поэтому твердосплавную пластину приходится делать достаточно толстой. Кроме того, вольфрамовый сплав плохо проводит тепло и сильно нагревается при работе. Из-за этого ухудшается качество обработки поверхности детали. Поэтому додумались слой сверхтвердого, сверхстойкого к износу материала наносить на подложку из твердой, как стекло, азотированной стали.
Однако для этого азот нужно внедрять в поверхность будущего резца строго там, где нужно, и в строго определенных количествах. Старинный процесс азотирования в железных ящиках этого сделать не позволяет.
Вот как эту задачу стали решать ученые из МГТУ СТАНКИН под руководством доцента Е.А.Чекаловой. Заготовку резца помещают в камеру со смесью азота и аргона вблизи катода из напыляемого металла (Ti; Сr; Zr) (рис. 3).

Между катодом и деталью создают высокое напряжение. Возникает дуговой разряд. Он создает облачко плазмы, состоящее из ионов и электронов. Вначале аргоном очищают и разогревают поверхность детали. Затем под действием электрического поля ионы азота начинают внедряться в ее поверхность. Примерно за 30–40 минут успевает образоваться твердый раствор азота в железе, но на возникновение вредных азотистых соединений времени не хватает. Таким образом возникает прочная азотированная поверхность, способная выдерживать значительное напряжение, возникающее при резании. Износостойкость его оставляет желать лучшего, но это ученых не беспокоит. На поверхность заготовки можно нанести слой, стойкий к износу. Он может быть очень тонким, ведь все действующее на него напряжение передается азотированному слою стали.
Поэтому совершенно не обязательно покрывать сталь слоем вольфрама. Годятся и гораздо более стойкие к износу карбиды титана и других металлов. Благодаря тому, что износоустойчивый слой очень тонок, он не успевает нагреться. Все тепло уходит. Качество обработки поверхности получается отличным. Таким образом ничтожное количество веществ, внедренных в кромку резца, словно витамины, облагораживает и продлевает его жизнь. Нет сомнения, что такая технология способна продлить и сроки службы валов, подшипников, зубчатых колес.
А.ИЛЬИН
Рисунки автора
У СОРОКИ НА ХВОСТЕ
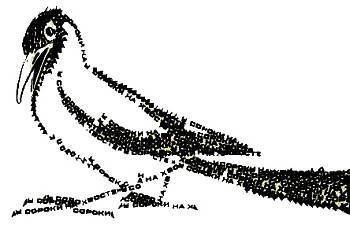
МОРСКИЕ ЕЖИ ПОДАРЯТ ЛЮДЯМ НОВЫЕ ЗУБЫ? Ученые из научного института Вайцманна (Израиль), изучив строение иголок морского ежа, пришли к выводу, что по аналогичной технологии можно выращивать зубы людям взамен утерянных. Дело в том, что морские ежи оказались обладателями своеобразных сумок из живых клеток, в которых карбонат кальция (кальцит) принимает нужную форму, затем кристаллизуется. Как только исследователи детально разузнают, как это происходит, человечество сможет навсегда отказаться от привычных приемов стоматологии.
ПЕРЕУЧЕТ АРГОНА. Специалисты южнокорейского Института стандартов уточнили содержание аргона в атмосфере. Его оказалось на 2 процента больше, чем считалось ранее по результатам измерений, которые проводились в 1969 году. Новые данные важны для прецизионных измерений массы атмосферы. Ведь аргон — один из самых тяжелых газов, ее составляющих. Поэтому средняя плотность воздуха, оказывается, выше примерно на одну сотую процента. Стало быть, настолько же больше стала и сила Архимеда, воздействующая со стороны атмосферы на окружающие нас предметы и нас самих. В итоге, скажем, килограмм железа должен теперь весить на 15 микрограммов меньше, чем считалось прежде.
КУПИ РАКЕТУ! В Японии создана ракета для розничной продажи частным лицам. Аппарат, сконструированный специалистами Университета Хоккайдо, весит 10,5 кг и имеет длину 1,6 м. По утверждению создателей, ракета многоразового действия с помощью двигателя на жидком кислороде поднимается на высоту в 1 км за первые 3 секунды полета. На борту она может нести полезный груз — например, видеокамеру массой около 500 г. По словам разработчиков, подобные ракеты послужат своеобразным дополнением к тем радиоуправляемым самолетам, кораблям и прочим моделям, которые продаются сейчас во всем мире. Правда, стоит новая «игрушка» около 19 тыс. долларов. Кроме того, каждый покупатель должен будет в обязательном порядке пройти двухдневное обучение основам безопасного запуска ракеты.